Following tests are done by us on insulated wire.
1. Dimension Test : Three measurements are made evenly distributed around the circumference of wire at each of two place 1 meter apart & the mean value of six results is calculated as overall diameter of wire. Similarly conductor diameter can be calculated by removing insulation by any method that does not damage conductor.
2. Electrical Resistance Test : This test is done by Resistance Meter wherein test reading at room temperature is taken and reading at 20°C is calculated .
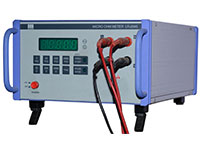
3. Elongation Test : To ensure that wire has flexibility– Essential for winding. The % values obtained should be more than values specified in relevant standard
4. Springiness Test : To ensure that when winding tension is released the coil retains its shape and size. The value in degrees obtained should not exceed value specified in relevant standard
5. Flexibility & Adherence Test : Peel test is done to ensure that the enamel film is not damaged during winding tension.
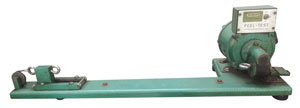
6. Heat Shock Test : Vital to ensure that the insulation can match the necessary temperature.A sample is prepared & placed in oven. When taken out after 30 minutes at specified temperatures, it shall show no cracks.
7. Cut through Test : In this test the thermo plasticity of the enamel film is checked under varying temperature and pressure.
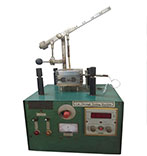
8. Solvent Test : In this test the effect of solvents on the enamel film is checked as the wire would come in contact with impregnating varnish, Transformer oil under varying temperature and pressure.
9. Breakdown Voltage : In this test a twisted sample is prepared under application of load.This test is done to ensure that insulation can match the necessary voltage.
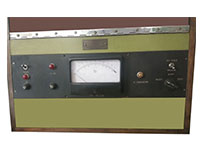
10. Continuity of Insulation : In this test the wire specimen with the conductor earthed is pulled over a “V” groove pulley which acts as a electrode & a DC test voltage is connected to electrode. This detects any micro bare points in the wire (to avoid any inter tern short circuiting in the coils).
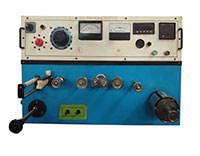
11. Temperature Index : In this test the temperature index is determined. The time for specified temperature to failure shall be not less than 5000 h exposure.
12. Abrasion resistance (Unidirectional) : This test is done to check that the enamel film is tough enough to withstand severest winding in high speed automatic winding machines.
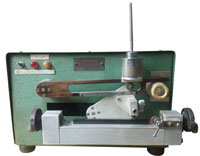
13. Tan Delta Bending Point : A very important test which indicative of good dielectric properties of insulation . This is generally required to optimise the processing parameters of the enamelling machine during production of enamelled wires. It informs about the curing condition of the wire. All the processing parameters have been standardised by us using this test.
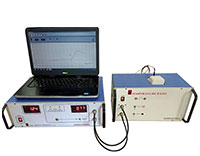
14. Shrinkage Test : This test is for shrinkage characteristic of submersible winding wires . The purpose of this test is to determine that such shrinkage does not cause any problem when the insulation gets heated due to energization.
15. High Voltage Test : The basic requirement of the insulation of submersible winding wire is to isolate the conductors from one another and withstand the voltage imposed on it when in service. This is ensured by High Voltage test in which a higher voltage stress is applied for a short duration.
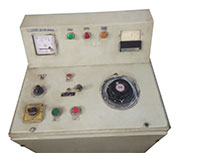
16. Insulation Resistance Test : This test on submersible winding wire is done to ensure the capability of manufacturing process as any flaw in the process will result in loss of dielectric properties of insulation.
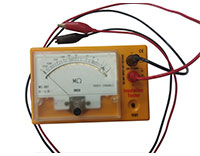